ก่อนอื่นต้องขออภัยครับที่หายไปนานพอสมควร
ช่วงเดือนกันยายนมีงานเข้าครับ ทำให้ต้องวิ่งสอนและเข้าปรึกษา
อยู่ต่อเนื่องตลอดทั้งเดือน
เช่นเคยครับ พักชมโมษณากันก่อน
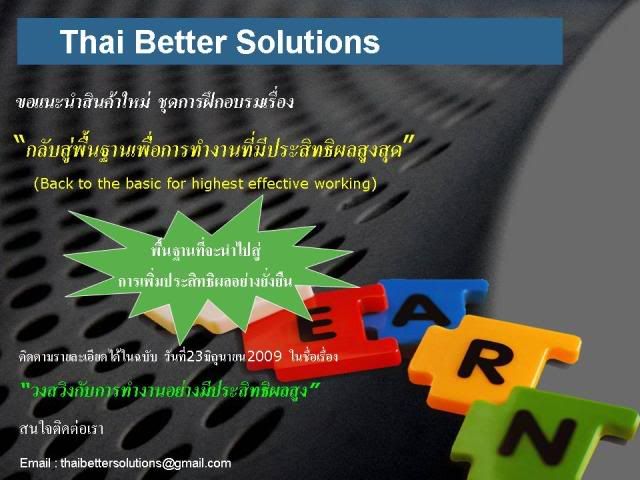
เรื่องนี้เกี่ยวข้องกันกับ “หัวข้อ 5W&2H คืออะไร” ครับ
โดยเฉพาะกับตัว What ทั้งเมื่อเกิดปัญหาหรือต้องวางแผนแก้ไขให้ดีขึ้น
เพราะว่าเมื่อเกิดปัญหาขึ้นมาไอ้เจ้าตัวปัญหานั้นล้วนมาจากตัวใดตัวหนึ่ง
(เป็นอย่างน้อย) ใน 5M&1E นี่แหล่ะที่เข้าไปสร้างให้เกิดขึ้น
และเมื่อจะแก้ไขปรับปรุงก็ต้องถาม What กับเจ้า 5M&1E นี่เหมือนกัน
ว่าจะทำอะไรกับมันดี จึงจะดีขึ้นได้
มีหลักการง่ายๆ ในการถามดังนี้ครับ
@ เมื่อเกิดปัญหา
ให้ถาม What happened (Changed)...
...เกิดอะไรขึ้นหรือเปลี่ยนแปลงกับ 5M&1E?
เป็นหลักทางวิทยาศาสตร์ง่ายๆ ครับ
ที่สิ่งของต่างๆจะคงสภาพเดิมของมันอยู่อย่างนั้น
ถ้าหากไม่มีปัจจัยภายนอกไปกระทำกับมัน สิ่งเหล่านั้นล้วนคือ Change ครับ
@ เมื่อจะแก้ปัญหา
ให้ถาม What shall we do...เราจะทำอะไรกับ 5M&1E?
ง่ายไหมครับ!!!
กระบวนการใดๆก็ตามครับ ไม่ว่าจะเป็นกระบวนการผลิต
กระบวนการควบคุมคุณภาพหรือแม้แต่กระบวนการทางธุรกิจ
ก็จะมีเจ้า 5M &1E เป็นปัจจัยอยู่เสมอ เพียงแต่เรามองมันออกหรือเปล่า
ว่ามันมีอยู่ และมีความสำคัญที่จะส่งผลกระทบให้ดีขึ้นหรือเลวลงก็ได้
แล้วแต่ว่าเราควบคุมมันหรือเปล่าและด้วยทิศทางไหน
วันนี้เรามาเรียนรู้จักมันครับ ที่สุดของพื้นฐานในการควบคุมกระบวนการ
M1) Material (วัตถุดิบ วัสดุช่วยงาน)
ความผิดปกติของวัตถุดิบ ที่เราต้องใช้หากผิดไปจากมาตราฐาน
ที่เราตั้งเอาไว้ย่อมสร้างปัญหาให้กับกระบวนการได้ครับ อย่างเช่น
ผิดรูปร่าง ผิดขนาด แตกร้าว เสื่อมสภาพเป็นต้น
M2) Man (พนักงานที่เกี่ยวข้องกับกระบวนการทั้งหมด)
การละเลยต่อหน้าที่ ต่อขั้นตอนหรือวิธีปฎิบัติงาน
ความเหนื่อยล้าจากการทำงานต่อเนื่องเป็นเวลานาน เป็นต้น
สิ่งต่างๆ เหล่านี้สร้างปัญหาได้ครับ
M3) Method (วิธีการปฎิบัติงาน)
การปฎิบัติงานที่ไม่มีวิธีการทำงานร่วมกันอย่างเป็นมาตราฐาน
และสอดคล้องกัน ต่างฝ่ายต่างทำตามอำเภอใจ หรือมีมาตราฐาน
แต่ไม่ได้รับการแก้ไขปรับปรุงให้เหมาะสมหรือทำให้การทำงาน
ดีขึ้นกว่าเดิม ก็ล้วนแต่สร้างปัญหาครับ
M4) Machine (เครื่องจักร เครื่องมือและอุปกรณ์ในการทำงาน)
การเสื่อมสภาพและการสึกหรอจากการใช้งานเกิดขึ้นได้เสมอครับ รวมถึงการเลือกใช้เครื่องจักรหรือเครื่องมือให้เหมาะสม กับลักษณะของงานตั้งแต่ต้น ก็มีความสำคัญไม่แพ้กัน
ฉะนั้นวิเคราะห์ถึงทางเลือกในการจัดหาเครื่องจักรให้ดีก่อน ที่จะลงทุนครับ และจัดระบบในการบำรุงรักษาให้ดี
M5) Measurement (เครื่องมือวัด และระบบการวัด)
ตัวนี้หลายคนมักละเลย ไม่ได้นำมาวิเคราะห์ถึงปัจจัยที่มีผลต่อ กระบวนการทั้งๆที่มันมีผลมากทีเดียว ลองคิดถึงการวัดระยะที่ต้องการ ค่าความละเอียดเพียงแค่ +/-0.10 มม. ดูสิครับ ถ้าไปเอาเครื่องมือวัด ที่มีความละเอียดมากกว่าหรือน้อยกว่ามาใช้จะเกิดอะไรขึ้น นอกจากนี้เมื่อเครื่องมือวัดใช้งานไประยะหนึ่งแล้วเกิดความคลาดเคลื่อนขึ้น โดยที่ไม่ได้รับการสอบเทียบ อีกทั้งหากมีเครื่องมือวัดมากกว่าหนึ่งตัว แล้วจะเชื่อถือตัวไหนว่าถูกต้องหล่ะ
พวกนี้สร้างโอกาสทำให้งานดีจะถูกตัดสินให้เป็นงานเสียและงานเสีย จะถูกตัดสินให้เป็นงานดีได้ทั้งสิ้น ใส่ใจต่อการเลือกความละเอียดที่เหมาะสม การสอบเทียบ ในระยะเวลาที่ไม่ทำให้เครื่องมือวัดผิดเพี้ยนไป และทำการสร้างสหสัมพันธ์ (Correlation) ให้กับมันครับ
*Correlation เป็นวิชาที่อยู่ในเรื่องระบบวิเคราะห์การวัด Measurement System Analysis ( MSA) ครับ*
E1) Environment (สิ่งแวดล้อมที่กระบวนการอยู่)
เป็นอีกตัวหนึ่งที่ไม่ค่อยเป็นที่รู้จักของสังคมอุตสาหกรรมส่วนใหญ่ ในบ้านเราเพราะถูกละเลยเต็มๆ ลองนึกถึงการผลิตนมพร้อมดื่มบรรจุขวด ใต้อาคารมุมสังกะสีสนินเขอะ ข้างถนนที่เต็มไปด้วยฝุ่นครับ พอจะนึกภาพออกไหม (ฮา !!!) และจะกล้าซื้อกินหรือเปล่า นี่เป็นตัวอย่างที่ยกมาให้เห็นภาพอย่างง่ายๆ ว่าในแต่ละอุตสาหกรรม ย่อมมีมาตราฐานถึงสิ่งแวดล้อมที่มันควรอยู่ครับ ทำมากกว่ามาตราฐานได้ (แต่เปลืองตังค์) แต่ทำน้อยกว่าไม่ได้
ที่กล่าวมาตั้งแต่ต้น ส่วนใหญ่ใช้หลักการจัดการอยู่สองเรื่องคือ
1) สร้างมาตราฐานที่จำเป็นในแต่ละเรื่อง
...เพื่อเป็นที่เข้าใจตรงกันของทุกฝ่ายที่เกี่ยวข้อง ว่าขั้นต่ำสุดที่รับได้ สำหรับกระบวนการของเราคืออะไร และแค่ไหน
2) ควบคุมและสอดส่อง (Control & Monitor)
...อย่างใกล้ชิดให้มั่นใจว่าทุกอย่างยังเป็นไปตามมาตราฐาน และหากพบสิ่งผิดปกติเกิดขึ้น ระบบสอดส่องต้องทำงานอย่างได้ผล ที่จะตรวจจับได้แต่เนิ่นๆ และส่งสัญญาณให้ผู้ที่เกี่ยวข้องได้รับรู้ทันท่วงที
อยากบอกว่า ธรรมชาติของ 5M&1E ก็เหมือนระเบิดเวลาครับ หากควบคุมมันได้ดีอยู่ นาฬิกาของมันก็จะหยุดเดิน แต่หากว่ามีอะไรหลุดการควบคุมหล่ะก็ เท่ากับต่อวงจรให้มันทำงาน และรอการระเบิดขึ้นนั่นเอง
ตื่นตัวอยู่เสมอนะครับ และหากสนใจที่จะเรียนกันเป็นเรื่องเป็นราว อย่างลึกซึ้งมากกว่านี้ ติดต่อ Thai Better Solutions ได้ครับ เรามีตัวอย่างที่สามารถประยุกต์ใช้ได้กับทุกธุรกิจและอุตสาหกรรม
สวัสดี
วางใจในมือที่เชื่อถือได้
Thai Better Solutions