ตั้งแต่วันที่ 10 กค ที่ผ่านมา
Six Big Losses (ความสูญเสียอันยิ่งใหญ่ 6 ประการ)
ที่ต้องรีบไปลดเพื่อการเพื่มประสิทธิผลโดยรวมของกระบวนการผลิต
เริ่มเลยนะ
ความสูญเสียอันยิ่งใหญ่ 6 ประการนี้นับได้ว่าเป็นสาเหตุพื้นฐานของ
การสูญเสียประสิทธิภาพต่างๆในการผลิต
เพราะว่ามันถูกวัดในเชิงประสิทธิภาพที่สูญเสียไปครับ
1) Breakdowns (การหยุดลงของเครื่องจักรจากความเสียหาย)
เป็น Loss ในมิติทางเวลาครับ เกิดขึ้นได้จาก
...breakdown ของเครื่องจักรเองที่พบเห็นเป็นประจำ
...การที่เครื่องมือหรืออุปกรณ์ที่ต้องใช้งานร่วมมีความเสียหาย
...การซ่อมบำรุงโดยไม่ได้วางแผน (unplanned maintenance)
# Loss ตัวนี้มีความวิกฤติสูงสุดทีเดียว เหตุเพราะว่าถ้าเครื่องจักรต้องหยุดลง
โดยไม่สามารถทำการผลิดได้ จะมีความหมายอะไรอีกเล่าที่จะไปลด
ความสูญเสียตัวอื่น (จริงไหม?) ดังนั้น Breakdown ต้องได้รับความใส่ใจ
อย่างมากในการวิเคราะห์ถึงสาเหตุที่เป็นรากเหง้าของปัญหา
และทำการถอนรากถอนโคนให้ได้
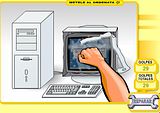
2) Setup and Adjustments (การติดตั้งและปรับแต่ง)
เช่นเดียวกันกับLoss ตัวที่1 ที่เป็นมิติทางเวลา เกิดขึ้นได้จาก
...การติดตั้ง/เปลี่ยนรุ่น (setup/changeover) การผลิต
...การขาดแคลนหรือหยุดลงของวัสดุและคนที่ใช้ในการผลิต
...การปรับแต่ง (adjustment) ใหญ่ที่ใช้เวลามาก
...การอุ่นเครื่องนานเกินไป
# Loss ตัวนี้เริ่มนับเวลาตั้งแต่ชิ้นงานดีตัวสุดท้ายที่ได้จากกระบวนการผลิต
ก่อนที่จะมีการหยุดเครื่องลง จนถึงงานดีชิ้นแรกที่ออกมาจากกระบวนการผลิต
ที่สามารถผลิตได้อย่างต่อเนื่องแล้ว (จำให้ดีและอย่าโกงนะ)
ฉะนั้นทุกครั้งที่มีการหยุดเครื่องลงไม่ว่าจะมาจากสาเหตุใด
(รวมถึง breakdown ด้วย)ก็ให้ใช้กติกาการนับอย่างนี้เป็นสากลที่ใช้กันทั้วโลก
# การจะลด Loss ตัวนี้ลงให้พุ่งเป้าไปยังโครงการ SMED
(Single Minute Exchange of Dies) พูดกันง่ายๆ ก็คือทำอย่างไรให้
การเปลี่ยนรุ่น/การปรับแต่งจบลงในเวลาหนึ่งตำแหน่งของหน่วยนาที
(ภายใน 9 นาที 59 วินาที นั่นเอง)
“การคิดว่าทำไม่ได้ก็เท่ากับปฏิเสธที่จะทำ” จริงไหมครับ !!!
ลองดู การแข่งขันรถยนต์สูตรหนึ่งที่เรียกว่า F1 (Formula 1)
ดูสิครับว่าเขาทำกันได้อย่างไร ที่ Pit Stop
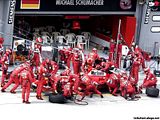
3) Small Stop (การหยุดเล็กน้อย)
นี่ก็อีกตัวครับที่ Loss ในมิติของเวลา เกิดขึ้นได้จาก
...การไหลของงานถูกกีดขวาง
...ชิ้นส่วนประกอบมีการติดขัด
...การป้อนงานผิดพลาด
...Sensor โดนบัง
...การส่งงานถูกสกัด
...การทำความสะอาด/ตรวจสอบ
# เกณฑ์ในการนับว่าเป็น Small Stop Loss ให้ดูจากการหยุดที่น้อยกว่า 5 นาทีและ
ไม่ต้องการทีมงานซ่อมบำรุงมาช่วยเหลือนั่นหล่ะ
แล้วจะจัดการอย่างไรดี ?
# ใช้หลักการวิเคราะห์ Cycle time ดูครับ เพราะมันคือเวลาที่ดีที่สุดในการได้ผลผลิต
หนึ่งชิ้นออกมาจากกระบวนการผลิต หากว่าเราใช้ Cycle time มากขึ้นนั่นหมายถึงมี small stop
มาเล่นซ่อนแอบกันแล้วหล่ะ ( เอ! หรือจะร่วมเล่นด้วยดี? คำตอบคงไม่นะครับ!!)
# ตามด้วยการทำบันทึกไว้ที่หน้างานเกี่ยวกับ small stop แต่อย่าเพิ่งหวังผลสูงมากนัก
เพราะมันมักเกิดขึ้นในช่วงเวลาอันสั้นและพนักงานมักจะไม่ค่อยลงบันทึกในรายละเอียดสักเท่าไร
เพียงแต่ขอให้รู้ถึงสาเหตุที่ต้องมีการหยุดเล็กน้อยเพื่อการสืบค้นหาต่อไปก็ยังดี
# สิ่งที่จะช่วยเรื่องนี้ได้ดีกว่าคือระบบการวิเคราะห์อัตโนมัติ ซึ่งต้องลงทุนสูงและใช้ผู้เชี่ยวชาญมาร่วม
สร้างระบบกับเรา ก็ดูกระเป๋าตังค์และความคุ้มค่าเอาเองนะ
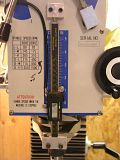
4) Reduced Speed (การสูญเสียความเร็วของกระบวนการผลิต)
อะไรก็ตามที่กีดขวางการกระบวนการผลิตไม่ให้ใช้ความเร็วสูงสุดตามที่คำนวณเอาไว้
ล้วนแต่เป็น Loss ประเภทนี้และเช่นกันมันเกี่ยวข้องกับเวลาครับ ตัวอย่างเช่น
...การเดินเครื่องโดยไม่ได้ปรับให้เข้าใกล้ความสามารถสูงสุดของเครื่องจักร
...การตั้งใจเดินเครื่องต่ำกว่า ความสามารถตาม Nameplate
...การตั้งใจเดินเครื่องต่ำกว่าการออกแบบ (Design Capacity)
...การสึกหรอของอุปกรณ์
...ความไม่มีประสิทธิภาพของพนักงาน
อย่างนี้ก็พบแต่ความสูญเสียนะสิครับ
ใช้การสำรวจตรวจสอบเทียบกับข้อมูลของเครื่องจักรหรือการออกแบบ
บวกกับการวิเคราะห์ Cycle time ดูครับแล้วก็ลงมือแก้ไขซ่ะ
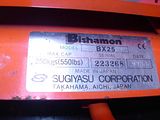
5) Startup Rejects (งานเสียที่จุดเริ่มต้นของการผลิต)
Loss ตัวนี้มีที่มาจาก Reject (rework หรือ scrap นับเป็น Reject นะครับ)
ทุกกรณีของกิจกรรมที่จุดเริ่มต้นการผลิต (Early Production)
ในทางทฤษฎีนับมันในหน่วยของเวลาครับเพราะว่างานทุกชิ้นมีเวลามาตราฐาน
ในการผลิตควบคุมอยู่แล้ว แต่ในทางปฏิบัติเพื่อความง่ายในการนับก็มักใช้
จำนวน Reject เป็นตัวนับในรูปของ Reject Rate
มันมีที่มาใหญ่ๆจากสองแหล่งคือ
5.1) การ Setup ที่ไม่ดีพอ
จาก Lossตัวที่ 2 การ Setup จะจบลงเมื่อกระบวนการนิ่งและเข้าสู่ Production เต็มตัว
แต่ถ้ามีความผิดพลาดจากการ Setupเกิดขึ้นหลังจากการผลิตไปได้ไม่นานจนทำให้เกิด Reject ขึ้น
ก็จะถูกนับอยู่ใน Startup Rejects ครับ ไม่นับใน Production Rejects
5.2) การอุ่นเครื่อง (Warm Up)
กระบวนการผลิตที่มีช่วงเวลาพักที่ต้องหยุดงานลงแล้วมา เริ่มต้นกันใหม่ด้วยการ
Warm Up กระบวนการนั่นแหล่ะครับคือที่มาของ Startup Rejects ประเภทนี้
และนับว่าเป็นสาเหตุใหญ่เสียด้วย กว่าจะผลิตงานดีได้อย่างต่อเนื่องก็มี
Reject บานตะไทเกิดขึ้น
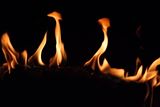
การลด Startup Rejects ก็ให้ไปควบคุมสองเรื่องครับ คือ
...พารามีเตอร์ที่ดีในการควบคุมการ Startup เพื่อลด Reject
...เวลาที่ใช้ในการ Startup ให้น้อยที่สุด
6) Production Rejects (งานเสียในระหว่างการผลิต)
Loss ตัวนี้มีที่มาเหมือนกันกับ Defect ในหัวข้อ 7 Wastes Reduction ฉบับวันที่ 15 กค 52 ครับ
ไปควบคุมปัจจัยที่มีผลต่อการเกิด Defect ก็จะลด Loss ตัวนี้ลง
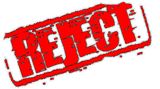
แล้ว Reject ต่างจาก Defect อย่างไร?
Defect เป็นลักษณะทางกายภาพของความบกพร่องที่เกิดขึ้นบนตัวชิ้นงานครับ
แล้วมาผ่านกระบวนการตัดสินว่าจะยอมรับ (Accept) หรือ ปฏิเสธ (Reject)
Accept ก็นำไปขายได้
Reject ก็นำไปแก้ไข (Rework) หรือ ทำลายทิ้ง (Scrap)
พอกระจ่างกันหรือยังครับ
ถ้ายังเข้าใจไม่พอที่จะนำไปใช้งาน ให้ Thai Better Solutions รับใช้คุณดีกว่าไหม
แล้วรอพบกับ OEE (Overall Equipment Effectiveness) กันครับ
สวัสดี